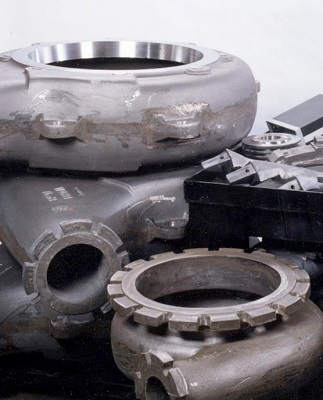
Industries such as mining, forestry and construction require the use of heavy-duty machines that are often subject to intense working conditions resulting in extreme wear and tear. In many cases, equipment wear parts made with steel castings are responsible for extending machine operating life and reducing downtime. These types of castings, for example, provide mining wear parts for a wide range of equipment including crushers, chute liners, mine car wheels and pumps. When resistance to heat or corrosion is needed, wear parts produced with stainless steel provide the solution. An Overview of Stainless Steels To be classified as corrosion resistant, stainless steel will contain a minimum of 10.5% chromium to provide additional resistance in aqueous environments where corrosion is a factor. The chromium content enables the formation of a protective film that increases corrosion resistance and, at higher temperatures, improves resistance to oxidation and enhances rupture streng
http://bit.ly/1QiPQB8