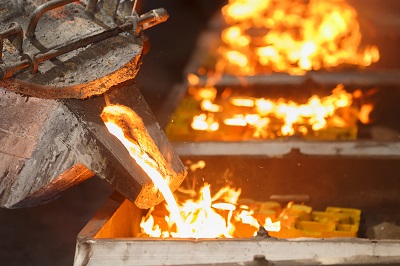
Due to excessive heat and friction involved in mining, corrosion and wear is one of the most prevalent problems in the industry. Millions are lost due to halted productions, worker injuries and unscheduled repairs as a result of wear and corrosion on equipment. Although replacement and repairs are an inevitable part of maintaining mining equipment, there are ways to minimise losses for continuous usage under harsh conditions. There are a number of methods that can slow down the effects of wear and corrosion particularly for crucial parts such as heat-resistant steel castings. Choice of Material The best way to ensure that parts will hold up against the pressure is to make them with excellent materials. Aside from strength, dent resistance, toughness and ductility, heat resistance should be a top characteristic for materials. Crafting parts using such materials will help improve its ability to resist breaking or wearing down under extreme temperatures.
http://bit.ly/1QpNsO8